Six Sigma ranks among the foremost methodologies for making business processes more effective and efficient. In addition to establishing a culture dedicated to continuous process improvement, Six Sigma offers tools and techniques that reduce variance, eliminate defects and help identify the root causes of errors, allowing organizations to create better products and services for consumers.
While most people associate Six Sigma with manufacturing, the methodology is applicable to every type of process in any industry. In all settings, organizations use Six Sigma to set up a management system that systematically identifies errors and provides methods for eliminating them.
People develop expertise in Six Sigma by earning belts at each level of accomplishment. These include White Belts, Yellow Belts, Green Belts, Black Belts and Master Black Belts.
How Six Sigma Began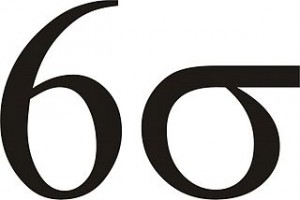
In the 19th century, German mathematician and physicist Carl Fredrich Gauss developed the bell curve. By creating the concept of what a normal distribution looks like, the bell curve became an early tool for finding errors and defects in a process.
In the 1920s, American physicist, engineer and statistician Walter Shewhart expanded on this idea and demonstrated that “sigma imply where a process needs improvement,” according to “The Complete Business Process Handbook: Body of Knowledge From Process Modeling to BPM Vol. 1” by Mark von Rosing, August-Wilhelm Scheer and Henrik von Scheel.
In the 1980s, Motorola brought Six Sigma into the mainstream by using the methodology to create more consistent quality in the company’s products, according to “Six Sigma” by Mikel Harry and Richard Schroeder.
Motorola engineer Bill Smith eventually became one of the pioneers of modern Six Sigma, creating many of the methodologies still associated with Six Sigma in the late 1980s. The system is influenced by, but different than, other management improvement strategies of the time, including Total Quality Management and Zero Defects.
Does it work? Motorola reported in 2006 that the company had saved $17 billion using Six Sigma.
What Six Sigma Means
Experts credit Shewhart with first developing the idea that any part of process that deviates three sigma from the mean requires improvement. One sigma is one standard deviation.
The Six Sigma methodology calls for bringing operations to a “six sigma” level, which essentially means 3.4 defects for every one million opportunities. The goal is to use continuous process improvement and refine processes until they produce stable and predictable results.
Six Sigma is a data-driven methodology that provides tools and techniques to define and evaluate each step of a process. It provides methods to improve efficiencies in a business structure, improve the quality of the process and increase the bottom-line profit.
The Importance of People in Six Sigma
A key component of successful Six Sigma implementation is buy-in and support from executives. The methodology does not work as well when the entire organization has not bought in.
Another critical factor is the training of personnel at all levels of the organization. White Belts and Yellow Belts typically receive an introduction to process improvement theories and Six Sigma terminology. Green Belts typically work for Black Belts on projects, helping with data collection and analysis. Black Belts lead projects while Master Black Belts look for ways to apply Six Sigma across an organization.
Methodologies of Six Sigma
There are two major methodologies used within Six Sigma, both of which are composed of five sections, according to the 2005 book “JURAN Institute Six Sigma Breakthrough and Beyond” by Joseph A. De Feo and William Barnard.
DMAIC: The DMAIC method is used primarily for improving existing business processes. The letters stand for:
- Define the problem and the project goals
- Measure in detail the various aspects of the current process
- Analyze data to, among other things, find the root defects in a process
- Improve the process
- Control how the process is done in the future
DMADV: The DMADV method is typically used to create new processes and new products or services. The letters stand for:
- Define the project goals
- Measure critical components of the process and the product capabilities
- Analyze the data and develop various designs for the process, eventually picking the best one
- Design and test details of the process
- Verify the design by running simulations and a pilot program, and then handing over the process to the client
There are also many management tools used within Six Sigma. Some examples include the following.
Five Whys
This is a method that uses questions (typically five) to get to the root cause of a problem. The method is simple: simply state the final problem (the car wouldn’t start, I was late to work again today) and then ask the question “why,” breaking down the issue to its root cause. In these two cases, it might be: because I didn’t maintain the car properly and because I need to leave my house earlier to get to work on time.
CTQ Tree
The Critical to Quality (CTQ) Tree diagram breaks down the components of a process that produces the features needed in your product and service if you wish to have satisfied customers.
Root Cause Analysis
Much like the Five Whys, this is a process by which a business attempts to identify the root cause of a defect and then correct it, rather than simply correcting the surface “symptoms.”
All the Six Sigma tools and methodologies serve one purpose: to streamline business processes to produce the best products and services possible with the smallest number of defects. Its adoption by corporations around the globe is an indicator of its remarkable success in today’s business environment.